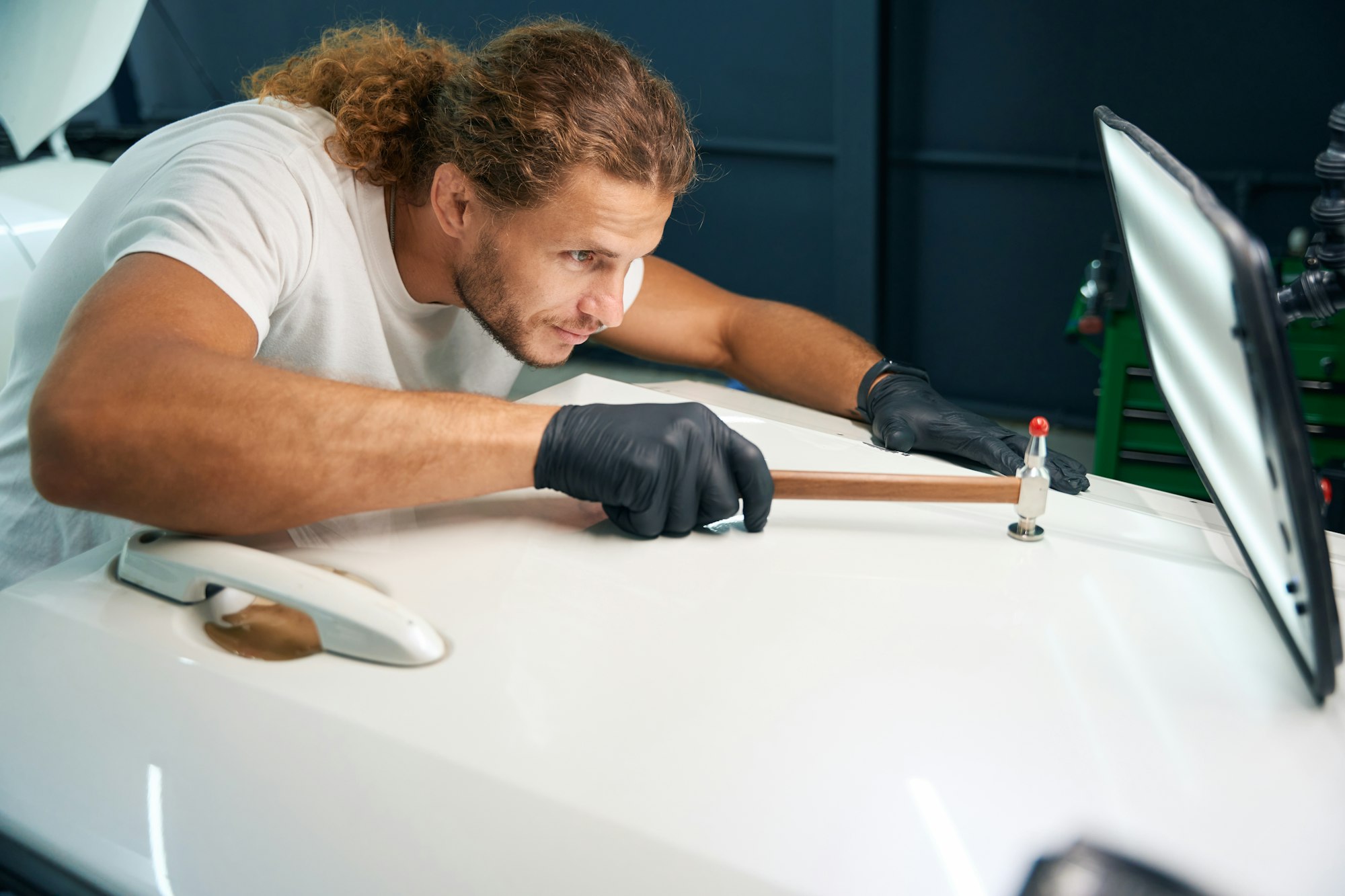
Paintless Dent Repair School: Learn the Craft of PDR
Paintless Dent Repair School: Learn the Craft of PDR with Our Paintless Dent Repair Training (PDR Training School) Welcome to the Paintless Dent Repair School
Paintless Dent Repair School: Learn the Craft of PDR with Our Paintless Dent Repair Training (PDR Training School) Welcome to the Paintless Dent Repair School
Paintless Dent Removal Training Near Me If you’re looking to advance your skills in Paintless Dent Removal, finding the right training program near you is
Searching for Paintless Dent Repair Training Near Me: Your Path to Becoming a Skilled Auto Technician from a PDR Training School Are you intrigued by
The automotive industry has always been at the forefront of innovation, constantly evolving to meet the demands of consumers. One area that has seen significant
Is It Better to Learn Paintless Dent Repair (Hands-on PDR Training) 1-on-1 or in Small Group with Multiple Instructors? Paintless Dent Repair “One-on-One”, hands-on training
Here at Paintless Dent Repair Academy, we receive testimonials from our past students on a daily basis. Overall the comments are words of thanks and
A true story. In the Paintless Dent Repair industry you will have plenty of opportunities to meet car enthusiasts. This is a hot market, so
If you are a PDR Technician already, then you know that it takes time to build a customer following. To build your reputation, you will